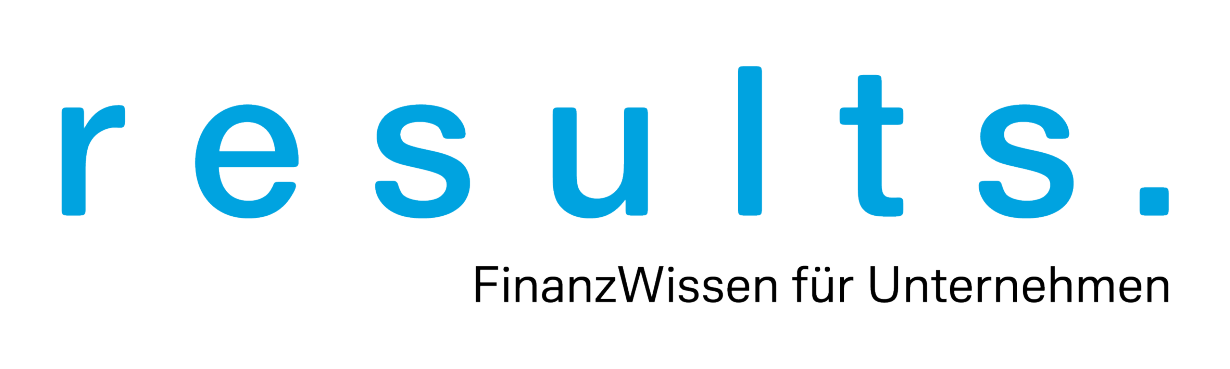
Wo bleibt die Industrie 4.0?
Vor mehr als 13 Jahren wurde die vierte industrielle Revolution ausgerufen. Doch in Deutschland setzt sie sich nur langsam durch. Woran liegt’s?
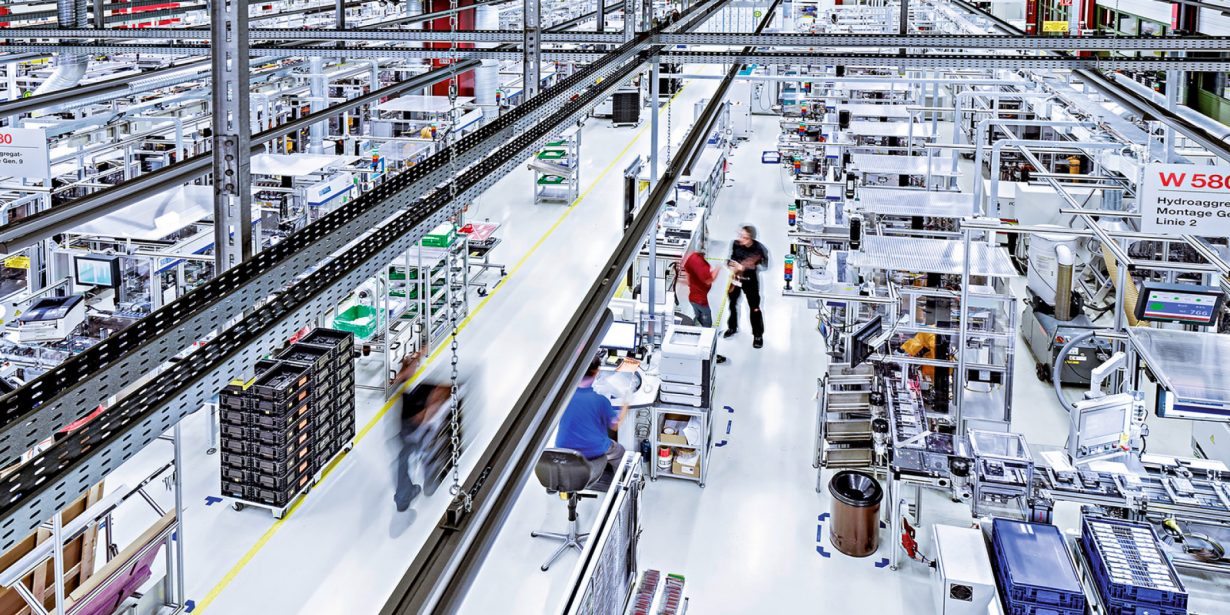
Geht doch: Industrie 4.0 in Deutschland, hier die „Connected Factory“ in Blaichach von Bosch. Foto: Bosch
Die Berater von BearingPoint hatten Ernüchterndes zu berichten: Von den rund 100 befragten Entscheidern aus deutschen Produktionsunternehmen hatte noch kein einziges eine echte Smart Factory umgesetzt. Zugleich sind 96 Prozent der Studienteilnehmer überzeugt, dass die Bedeutung der Industrie 4.0 steigen wird. Und 81 Prozent planen, in den kommenden Jahren entsprechend zu investieren. Das Problem: Diese Zahlen stammen nicht aus der Frühzeit der Industrie 4.0, sondern wurden Anfang dieses Jahres veröffentlicht. Was ist geschehen, seit 2011 auf der Hannover Messe die Revolution ausgerufen wurde?
Auch Dampfmaschine, Elektrifizierung und Digitalisierung haben sich nicht über Nacht durchgesetzt. Doch wer Mitte des vergangenen Jahrzehnts Industriemessen besucht hat, konnte den Schlagworten Industrie 4.0 oder Smart Factory kaum entkommen. Stolz wurden vernetzte Fertigungsprozesse ausgestellt, war die Rede von Losgröße 1 und Predictive Maintenance. Erstmals würde eine Vernetzung der gesamten Wertschöpfungskette erlauben, effizienter zu planen. Maschinen könnten sich selbst regeln, Wartungsbedarf vor dem Ausfall anmelden und den Output optimieren. Der Mensch würde nur noch eine Aufsichtsrolle einnehmen – oder ganz aus der Fabrik verschwinden. Die Industriekapitäne waren von den neuen Möglichkeiten begeistert.
China vorne in der Smart-Factory-Umsetzung
Deutsche Konzerne begannen mit der Errichtung von Vorzeigefabriken. Bosch betreibt die „Connected Factory“ in Blaichach, Siemens hat das „Elektronikwerk“ in Amberg, Infineon in Dresden eine Smart Factory. Adidas hat ab 2015 in Ansbach und Atlanta gemeinsam mit dem strategischen Partner Oechsler Motion zwei „Speedfactories“ aufgebaut, die schneller, individueller und effizienter Sportschuhe herstellen als bislang möglich war. Im Frühjahr 2020 wurden beide geschlossen, die Technologie soll nun bei Zulieferern in Asien eingesetzt werden.
„Es ist einfacher, wenn Tesla eine neue Fabrik in Brandenburg von Null aufbaut, als einen laufenden, etablierten Betrieb umzubauen.“
Frank Niemann, Deutsche Bank
Obwohl Deutschland den Begriff Industrie 4.0 geprägt hat, hat heute in der Umsetzung Asien die Nase vorn. Südkorea will beispielsweise bis 2025 mindestens 1.000 Smart Factories staatlich gefördert haben. Aber vor allem China dominiert inzwischen das Thema. So wurden dort bis Ende 2023 nach offiziellen Angaben 421 Demonstrationsfabriken auf nationaler Ebene und über 10.000 digitale Werkstätten und intelligente Fabriken auf Provinzebene gegründet. Allein Schanghai will in diesem Jahr 70 weitere Smart Factories auf dem Stadtgebiet errichten.
Der Abstand ist inzwischen riesig
Das meiste sind isolierte Versuchsanordnungen. Aber nicht alle. Die China Baowu Steel Group will bis 2026 über 10.000 neue Roboter in der Fertigung einsetzen, die an eine smarte Cloud-Plattform angeschlossen sind. Kunden der Marke Maxus des chinesischen Autoherstellers SAIC können innerhalb weniger Minuten aus tausenden Optionen auswählen – ohne Zusatzkosten. Anschließend können sie in Echtzeit verfolgen, wie weit die Herstellung ihres individuellen Autos gediehen ist. Möglich machen das smarte Logistik und Fertigung, die auch die digitale Anbindung hunderter Zulieferer umfasst.
Von den 153 Fabriken, die Eingang in das „Global Lighthouse Network“ der „am weitesten entwickelten Fabriken der Welt“ des World Economic Forum fanden, sind 62 chinesisch. Chinas Vormachtstellung zeigt auch das aktuelle Industrie-4.0-Barometer der Prozess- und IT-Beratung MHP aus diesem Frühjahr: 94 Prozent der Befragten in China geben an, bereits KI-basierte Lösungen in Fertigungsprozessen einzusetzen. In der DACH-Region sind es lediglich 20 Prozent. 66 Prozent der chinesischen Teilnehmer setzen bereits teilweise oder vollständig Ortungstechnologien ein. Die können zum Beispiel helfen, den Produktionsfortschritt eines Teils zu verfolgen. In der DACH-Region: 36 Prozent. So geht es weiter, ob beim digitalen Zwilling der Fabrik, KI in der Fertigung oder dem Einsatz autonomer Maschinen und Roboter. Am deutlichsten wird der Abstand bei der Frage, bei wem selbst handelnde, steuernde und sich verbessernde Maschinen oder Roboter noch nicht eingesetzt werden. In China sind das gerade einmal 2 Prozent der Fälle, in der DACH-Region 41 Prozent.
Was hemmt deutsche Unternehmen?
Es mangelt (bei der Mehrheit) nicht an Einsicht, dass Industrie 4.0 für die eigene Fertigungszukunft entscheidend ist. Der Investitionswille ist vorhanden, auch wenn er in den vergangenen Jahren von der Corona-Pandemie und gleich darauf von der Energiekrise überlagert und ausgebremst worden ist. Kapital zumindest dürfte dennoch oftmals vorhanden sein, lange haben deutsche Unternehmen komfortable Gewinne erzielt: Mitte 2023 meldete die OECD, dass hierzulande die Stückgewinne seit 2019 stärker gestiegen sind als in den meisten anderen Industrieländern. Die Unternehmen selbst – nach den Gründen für die Verzögerungen in der Umsetzung befragt – nennen zumeist den Fachkräftemangel. Auch vorhandene veraltete oder inkompatible Software-Systeme und die Schwierigkeiten der Einbindung ins Tagesgeschäft spielen laut MHP-Industrie-4.0-Barometer eine große Rolle. Allerdings macht MHP dafür nur globale Angaben. Zugleich bekommen Unternehmen die Hemmnisse aber langsam in den Griff; in den Vorjahren lagen die Werte global noch höher.
Für Deutschland dürfte das kaum gelten, der Fachkräftemangel wird sich eher noch verschärft haben. Auch verfügt Deutschland über eine „historisch“ gesehen deutlich modernere, professionellere Fertigung als China früher. Das bedeutet zugleich, dass der Erneuerungsdruck nicht so hoch sein mag. Die chinesische Changying Precision Technology hat 2015 ihre 600 Fabrikarbeiter durch 60 Roboter ersetzt. Danach stieg die Produktivität um 250 Prozent, der Ausschuss sank um 80 Prozent. Kaum vorstellbar, dass solche Fortschritte in den Fabriken am Hochlohnstandort Deutschland erzielt werden könnten.
... mich für den monatlichen Newsletter registrieren.
Spannende Informationen und relevante Themen aus der Wirtschaft und Finanzwelt in kompakter Form für Ihren unternehmerischen Alltag und für Ihre strategischen Entscheidungen.
Wir machen Wirtschaftsthemen zu einem Erlebnis.
Das Silo-Problem
Vielleicht ist der Innovationssprung einfach nicht so groß, der Handlungsdruck geringer? Eike Bieber, IT- und Digitalexpertin von der Deutschen Bank widerspricht: „Auch in Deutschland sind viele Prozesse noch von Medienbrüchen geprägt, weil heterogene Strukturen über Jahre gewachsen sind. Da gibt es noch so manche Möglichkeiten, die nicht unbedingt großen Aufwand verursachen.“ Deutsche Produktionsunternehmen sind weltbekannt dafür, dass sie ihre Fertigung permanent verbessern. Doch darin kann eine Schwäche liegen, weil der Sinn verloren gegangen sein könnte für grundlegende Veränderungen. „Es ist einfacher, wenn Tesla eine neue Fabrik in Brandenburg von Null aufbaut als einen laufenden, etablierten Betrieb umzubauen“, weiß ihr Teamkollege Frank Niemann von der Deutschen Bank.
Es braucht aber für Industrie 4.0 eine gedankliche Revolution statt einer Evolution: Die Stärke der Smart Factory liegt aber eben nicht in der Optimierung des einzelnen Fertigungsschritts, nicht einmal des einzelnen Prozesses. Sondern in der übergreifenden Betrachtung der Wertschöpfungskette. Dazu muss die Perspektive gewechselt werden. Das ist gar nicht so einfach. Beispiel Daten: Oft genug werden zwar sehr viele Daten gesammelt, aber nicht geteilt. Sie bleiben in Datensilos. Dafür gibt es nachvollziehbare Gründe: Technische Inkompatibilität; der Wert der Daten für Andere ist unbekannt; sowie datenrechtliche Sorgen. Gerade für Datenschutzbedenken ist Deutschland bekannt, doch das MHP-Barometer zeigt: Regulatorische Vorgaben erschweren es chinesischen Fertigungsbetrieben noch stärker als deutschen, Daten mit externen Partnern auszutauschen. Allerdings nennen auch 40 Prozent der DACH-Unternehmen, dass fehlender Datenaustausch mit Partnern entlang der Wertschöpfungskette die Umsetzung von Industrie 4.0 verzögert.
Industrie 4.0 machen, nicht drüber reden
Die Umsetzung der Industrie 4.0 braucht Zeit. Doch wahrscheinlich sind wir in Deutschland schon vielfach weiter, als die Daten zeigen. „Viele Unternehmen sprechen von Automatisierung, machen aber schon Industrie 4.0, zumindest in Teilen“, stellt Niemann fest. Kollegin Eike Bieber stützt diese Einschätzung: „Wenn man deutsche Hersteller fragt, ob sie eine auf einer Messe stolz vorgestellte neue Technologie auch schon einsetzen kommt oft genug die lapidare Antwort: ‚Das ist für uns schon längst Alltag.‘ Viele Unternehmen machen mehr als sie öffentlich kommunizieren.“
Dennoch bleibt insbesondere die übergreifende Vernetzung innerhalb des gesamten Shopfloors und darüber hinaus eine große Herausforderung. Das alles sind allerdings keine neuen Erkenntnisse. Und sie bleiben abschreckend – vor allem für die, die sie in der Praxis umsetzen sollen: Habe ich nach der Transformation denn noch eine Arbeit in der Fabrik? „Unternehmensführungen müssen viel stärker aufzeigen, dass Industrie 4.0 mehr ist als Kosteneinsparungen – sondern allen im Betrieb neue Möglichkeiten eröffnet“, sagt Niemann. Allerdings ist auch das gar nicht so einfach, denn viele Kunden möchten beispielsweise weiterhin nur eine Maschine kaufen (und abschreiben) und keine flexiblen Benutzungsentgelte zahlen.
Auch wenn die Umsetzung nicht so rasch passiert wie anfangs gedacht, ist Industrie 4.0 nicht tot. Im Gegenteil, die Unternehmen verstehen immer besser, dass es ohne die digitale Transformation nicht geht. Auch das ist ein Ergebnis der MHP-Erhebung: Nur noch 43 Prozent der weltweit Befragten nannten zuletzt Unsicherheit beim Return on Investment als Grund für Verzögerungen. Nur ein Jahr zuvor waren es noch 67 Prozent gewesen. Die Vorzeichen sind gut, dass die 4. industrielle Revolution an Fahrt aufnimmt, auch in Deutschland.
08/2024
Chefredaktion: Bastian Frien und Boris Karkowski (verantwortlich im Sinne des Presserechts). Der Inhalt gibt nicht in jedem Fall die Meinung des Herausgebers (Deutsche Bank AG) wieder.